樹脂射出成形やダイカストの金型をお使いの場合。
スライドコアが焼き付いて動かなくなった、または製品にバリが出て使い物にならない。
という経験があると思います。
金型屋さんはもちろんですが、成形される方も気を付けていただければトラブルがグッと減ると思いますよ。
スポンサーリンク
結論:予防することが、一番の対策
一度起こってしまってからは、修復は難しいです。
下手すると、その周辺が作り替えになってしまうことすらあります。
傷んだ部分を滑らかに整えても再発することは多いですね。
レーザー溶接で修理すればかなり綺麗に仕上がります。でも、またすぐに荒れてきてしまうんですよね。
人間の病気と一緒です。
結局、予防が一番安上がりです。急がば回れです。
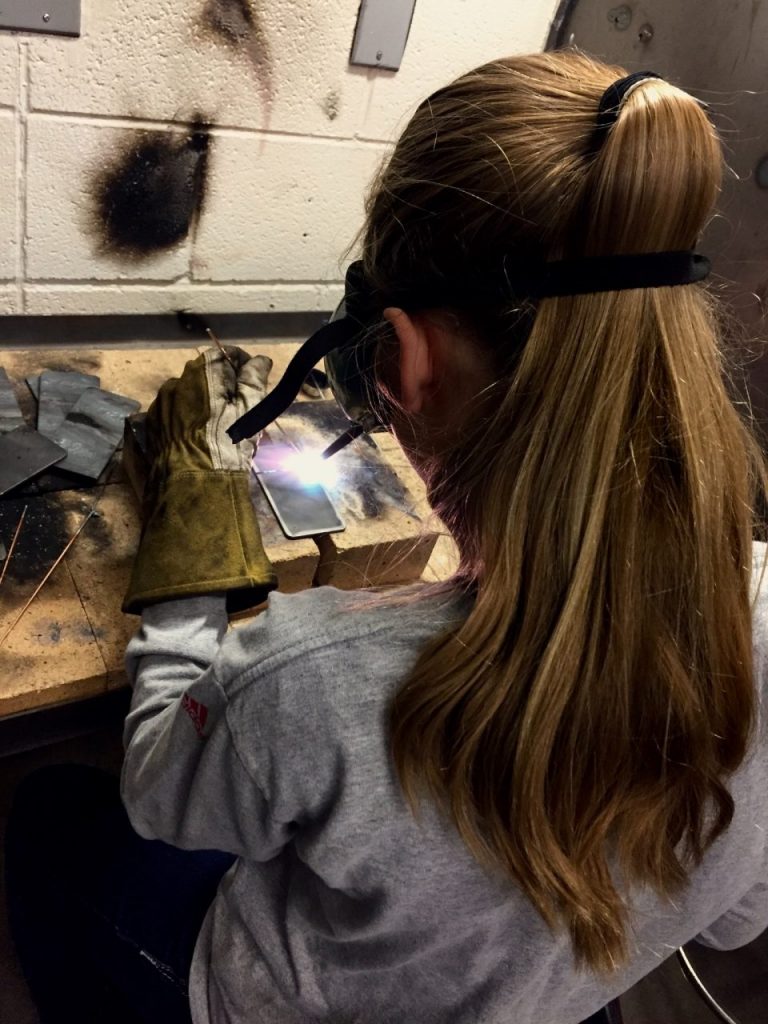
新品の金型はチェックしましょう
各部のボルトはきちんと締まっているか
あれ? 関係ないでしょと思われたかもしれません。
元々の精度が悪いせいで、ボルトを締めると動かなくなる金型もあるのです。
下記がよくあるポイントです。
- スライドのレール
- エジェクタガイドピン
- ランナーガイドピンやセンターピンの固定ボルト
型の開け閉め
- 自然な力で開け閉めできるか?
- 変な音や振動はないか?
スライドの動き
- 軽く動くか?
- 突き当て部までスムースで、”コン”と音がするか?
- 摺動面には油溝が加工されているか?
押し出し板
- スムースに突き出しできて、変な音はしないか?
- 元に位置までスッと戻るか?
職場にダイスポプレスがあれば、すぐに確認できますよね。
もし無ければ、成形機に取り付けて動かしてみる。
または、スプリングを抜いて定盤の上で手で動かしてみることになりますね。
使う前に悪いところを治しておきましょう
- 摺動面に油溝を加工する
- 隙間が狭すぎる部分を調整する
- 穴が曲がっている、傾いている等の修正
(大掛かりになる可能性もありますね。)
金型が新品の時にみがいておきましょう
表面をすべすべにする
”焼き付き”という言葉からわかるように、2つの部品の金属が熱で一瞬溶けて混ざり合うわけです。
その熱がどこから来るかというと、圧力です。
何の圧力かと言うと、ザラザラな表面の凸と凸の先端がぶつかり合って押し付けられるんですね。
ここで最近感じていたのですが、マシニングセンタや工具の進化によって加工目が綺麗になってきたのも原因の一つかなと。
いや綺麗なことが原因ではなくて、中途半端にきれいに見えるから磨いていないんですよね。
綺麗に見えても、やはりミクロのレベルで凸凹やかえり的な物はあるわけで。
サッとでもよいから磨いておくと、かなり違うように思うんですよね。
角を”ほんのり”丸くする
金型はバリが出ないように”角”になっていなければなりません。
でも、シャープな角だとかじってしまって焼き付きの原因になるんです。難しいですね。
そこで、見えるか見えないかというレベルでわずかに丸みを付けておくことが対策になります。
#1200くらいのサンドペーパーでするっと撫でるイメージでしょうか。
きれいに掃除する
もしかすると、これが一番大事かもしれません。
磨きの時に発生した非常に細かいクズが、焼き付きの原因になることも少なくないです。
わずかに焼き付き始めた部分が、短時間に一気に悪化する原因はこれです。
きれいな定盤の上で、きれいなウエスを用意。
洗浄剤を吹きかけて、隅は綿棒を使うなどして粉をきれいにふき取ってください。
よく、洗浄剤をかけた後でエアガンで吹き飛ばせばOKだと思っている方がおられます。
しっかり見てください、全く取れていないですよ。
製品に影響しない範囲にはグリスなどを塗る
きれいにしたら、製品部分から遠い所の摺動部分にはグリスを塗っておきましょう。
ただし、高い温度(180℃)で使うような金型の場合は耐熱グリスを使って下さいね。
通常のグリスを塗っていると、成形時にモクモク煙が上がって大変なことになります。
(昔、知らずに使って怒られました。)
一度トライ成形した後の金型も要チェック
納品前に最善を尽くしていたとしても、トライから帰ってきた金型も要チェックです。
スライドなどに擦り傷が出ていれば、油溝の周囲が角ばっているのかもしれません。
これが意外と、かじりに直結します。
また、部品同士の突き当て部も要チェック。
当たり方が強い時などに、先端がわずかに潰れて角に小さなかえりが出ていることがあります。
金型設計時点でできること
焼き付き難い構造にしておく
- すり合わせるのではなく、突き当てる型割りとする
- 一定幅の溝をスライドさせるのではなくテーパで合わせる
- 摺動部には油溝を設ける
- スライドコアにも冷却回路を設ける
- 不可能な場合は、隙間を多めにする(熱膨張を計算)
鋼材の硬度を工夫する
- 予算の範囲内で、できるだけ高い硬度とする(HRC60以上)
- HRC50以下の場合は、合わせる部品の硬度に差を設ける
- 同じにせざるを得ない場合は、片方に表面窒化をする
剛性を確保する
- 板に厚みを持たせて、剛性を確保する
隙間が確保される寸法設定にしておく
- 熱膨張を考慮して隙間を設定する
- 図面は-0.01/-0.02などの片振れ公差ではなく、図形の
寸法自体を29.98などのマイナスにしておく
※金型屋さんによっては、公差を無視して隙間を最小に
詰めて仕上げてしまうところがある
磨いてもらうよう図面指示する
- スライドの溝や、油溝部分に”みがき”を図面に明記する
(意外と、加工後の微小なかえりが取られていないことがあります)
焼き付きの原理を知っておこう
原理を知っておけば、見る目が変わって気が付きやすくなると思います。
焼き付き(かじり)の種類
アブレシブ磨耗
擦れ合って、表面がザラザラの時に硬い方が柔らかい方を削ってしまうことにより起こります。
削ってしまうこと自体に加えて、それにより発生した粉がさらに摩耗を進めてしまいます。
焼き入れで硬度をあげることや、表面窒化が有効です。
凝着磨耗
ザラザラの凸が擦れ合って熱で溶けて一体したところで、むしり取られて起こります。
これもむしり取られた時に粒が発生して、さらに破壊が進みます。
アブレシブ磨耗 よりも派手に進行します。

同種の金属の場合に起こりやすいので、対策はメッキや表面コーティングを施す。
また、二硫化モリブデン入りグリス塗布などで、金属同士が接触しないようにすることも有効です。
疲労磨耗
スライドコアなどが、動いたり止まったりを繰り返すうちに表面が疲労します。
それにより細かいクラック(割れ)が入ることで、魚のウロコ状の粒が発生しまして焼き付きとなっていきます。
対策は、傷み易い部分は交換できる構造にしておくことではないかと思います。
以上、参考になればうれしいです。
精神論のようになってしまいますが、この辺りを細かくチェックされる成形屋さんの金型は、いつまでも美しいです。
また、焼き付きなどのトラブルで修理に出されることもほとんどありません。
最後までお読みいただきまして、ありがとうございました。
スポンサーリンク